High Pressure Gas Quenching: The Key to Long H13 Insert Life
HPGQ vacuum furnaces have the ability to harden parts of various materials, sizes, and geometries, in a clean, efficient, and effective way, including hand tools, gears, bearings, shafts, etc.
HPGQ (High Pressure Gas Quench) has a number of key design features that provide this capability. For instance, the SECO/VACUUM Vector® design features:
- Uniformity - 360 deg. arrangement of nozzles with front wall nozzle assembly and rear exit provides uniform flow around full working zone
- Quench gas velocity - 40-50 m/s (111 mph - Category 3 hurricane) provides better gas penetration into working zone than hatch or door designs - higher velocity at the work surface = better heat transfer
- Pressure (SVT offers up to 25 bar)
- Gas (SVT = N2, He, H2)
- Heat exchanger - high efficiency heat exchanger ensures a consistent temperature difference during the quench
- This style of furnace has the potential to provide a highly effective quench for a wide range of parts
Contact SECO/VACUUM to learn how a Vector® vacuum furnace
with HPGQ can improve your heat treatment quality.
- Die Insert Challenge
- NADCA Standard
- NADCA Block Test
- SECO/VAC Quench Performance
- SECO/VAC Quench Software
Quenching large cross sections on die inserts is a challenge. These die inserts often use H11 or H13 steel which present a number of challenges:
- Uses a deeply hardenable steel which hardens easily and sometimes has thick cross sections to 16”
- Needs high surface hardness to provide reasonable wear, while retaining a ductile core for toughness
- Must maintain tight geometry tolerances – to meet geometry needs
There are many failure causes from Heat treating cycles on End users (automotive manufacturers) carefully analyzed these failures and isolated the causes.
- Cracking
- Distortion
- Carbide formation
- Incorrect microstructure
- Softening
- Heat checking
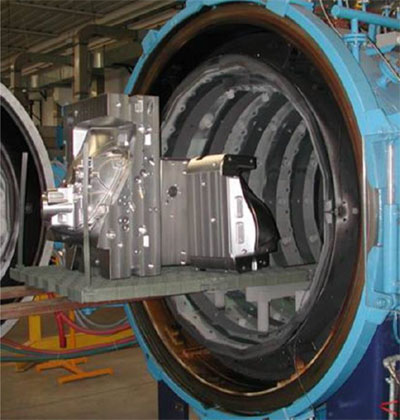
Heat treating is the most common cause of failure. The issues arise from a lack of full austenitization or poor quenching due to these causes, i.e.:
- Too much time at austenitizing temp.
- Large ΔT during heat treating
- Release of stresses during operation
- Too much time between hardening and tempering operations
- Application related cracking due to inadequate core ductility
- Non-uniform quench
- Inadequate quench speed (heat checking)
GM, Ford and NADCA all created industry standards. The NADCA standard includes a quench specification as follows: Rapid Quench (50 F/min minimum) with 3 tempers (2 hrs. each) – immediately (2-3 hrs. for large cross section). Key parts of the standard are:
- Microstructure development via the austenizing temperature to 1885°F
- Toughness from the quench speeds of ≥ 50°F/min. to 1000°F for the die surface
- Geometric Stability for Core Ductility for Quench Uniformity and Stabilization via Isothermal (or interrupted) quench at 800°F until Ts and Tc are within 200°F or 30 min maximum
- 16” x 16” x 16” block
- H13 tool steel
- Surface thermocouples placed on each face of block
- Hole diameter to match OD of thermocouple wire used
- Hole depth: 0.625” +/- 0.125”
- Core thermocouple placed in hole extending to the center of the block
- Block positioned in the center of the furnace to simulate actual die quenching
- NADCA notes that cross sections > 16” may limit quenching speeds in certain equipment
- This allows quenching performance among different furnace manufacturers to be compared
The NADCA block test showed that the SECO/VACUUM furnace performed two times faster than the required quench test. Smaller furnaces produce faster quench rates due to higher gas velocity in contact with block. Plus, an increase in pressure and a corresponding increase in density improves cooling; furthermore, Helium’s thermal conductivity is nearly 6 times that of nitrogen which doubles the quench speed.
Note:
- Data taken from a 36” x 36” x 60” SECO/VACUUM 15 bar
- T/C moved during quench on right face
Quenching software tools are now also available to simulate this process. SECO/VACUUM G-Quench software has a built in library of materials and furnace configurations that can be used to supplement the real world tests. See example modeling below: Red line is NADCA.
Vacuum Furnace Processes
Fine Carb®: Vacuum Carburizing High Pressure Gas Quench High Vacuum Furnaces PreNit: High Speed Vacuum Carburizing Vacuum Brazing: Advanced Front Loading Gas Nitriding with ZeroFLow® SECO/PREDICTIVE SECO/PREVENTIVE
Specifications Subject to Change without Notice
